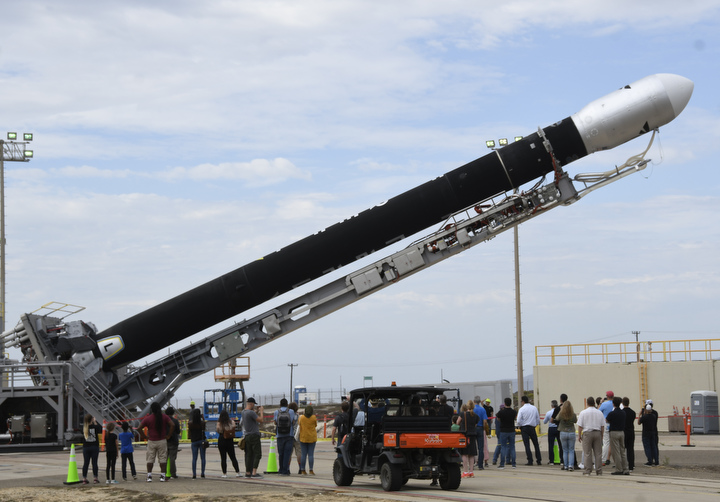
08 Feb ROCKET RAISING HYDRAULIC CYLINDERS
Rocket raising hydraulic cylinders play a crucial role in the aerospace industry, facilitating the precise and controlled elevation of rockets during assembly, integration, and launch preparations. These specialized hydraulic cylinders are designed to withstand extreme loads, temperatures, and environmental conditions while ensuring the safety, reliability, and efficiency of rocket lifting operations. This essay explores the innovations and design considerations driving the development of rocket raising hydraulic cylinders, highlighting key principles, challenges, and emerging trends in the field.
Performance Requirements and Challenges:
Rocket raising hydraulic cylinders operate in demanding environments characterized by high loads, tight tolerances, and stringent safety requirements. These cylinders must exhibit robust structural integrity, precise motion control, and reliable performance throughout the rocket lifting process. Moreover, they must withstand exposure to corrosive fluids, temperature variations, and dynamic loads associated with launch operations.
Advanced Materials and Construction Techniques:
To meet the performance demands of rocket raising applications, hydraulic cylinder manufacturers employ advanced materials and construction techniques. High-strength alloys, such as steel and aluminum, are commonly used to withstand the high-pressure hydraulic fluid and mechanical loads experienced during rocket lifting operations. Advanced welding, forging, and machining processes ensure the integrity and durability of cylinder components under extreme conditions.
Customized Design and Engineering Solutions:
Rocket raising hydraulic cylinders are often customized to meet the specific requirements of launch facilities, rocket configurations, and operational scenarios. Engineers collaborate closely with aerospace stakeholders to design cylinders that optimize lifting capacity, stroke length, and speed while minimizing footprint, weight, and energy consumption. Computer-aided design (CAD) software and finite element analysis (FEA) tools enable accurate modeling, simulation, and validation of cylinder performance under various loading conditions.
Precision Motion Control and Positioning:
Accurate motion control and positioning are critical aspects of rocket raising hydraulic cylinder design. Hydraulic systems incorporate precision valves, actuators, and feedback mechanisms to regulate fluid flow, pressure, and cylinder movement with high accuracy and repeatability. Closed-loop control systems leverage sensors, encoders, and feedback algorithms to monitor and adjust cylinder position, velocity, and force in real-time, ensuring smooth and synchronized rocket elevation.
Safety and Redundancy Features:
Safety is paramount in rocket lifting operations, necessitating the integration of redundant systems, fail-safe mechanisms, and emergency stop protocols into hydraulic cylinder designs. Redundant hydraulic circuits, pressure relief valves, and mechanical locks provide backup measures to prevent uncontrolled descent or catastrophic failure during rocket lifting and lowering procedures. Comprehensive risk assessments and failure mode effects analyses (FMEAs) guide the implementation of safety features and mitigation strategies throughout the design lifecycle.
Environmental Considerations and Sustainability:
In an era of increasing environmental awareness and sustainability concerns, rocket raising hydraulic cylinder design incorporates eco-friendly materials, energy-efficient components, and lifecycle optimization strategies. Manufacturers explore alternative hydraulic fluids, such as biodegradable oils and synthetic lubricants, to reduce environmental impact and comply with regulatory requirements. Additionally, energy recovery systems, regenerative braking, and smart control algorithms enhance energy efficiency and minimize carbon footprint during cylinder operation.
Integration with Automated and Robotic Systems:
Advancements in automation and robotics are reshaping the landscape of rocket lifting operations, driving the integration of hydraulic cylinders with automated assembly, integration, and launch platforms. Collaborative robots, gantry systems, and autonomous vehicles coordinate the movement and positioning of hydraulic cylinders in a synchronized and efficient manner, streamlining workflow processes and reducing human intervention. Real-time data exchange and communication protocols enable seamless integration and interoperability among diverse aerospace systems and subsystems.
Rocket raising hydraulic cylinders represent a critical component of aerospace infrastructure, enabling the safe and reliable elevation of rockets during assembly, integration, and launch preparations. Innovations in materials science, design engineering, motion control, and safety technology have revolutionized the performance and capabilities of hydraulic cylinders in rocket lifting applications. By embracing advanced materials, precision engineering, and sustainability principles, hydraulic cylinder manufacturers continue to push the boundaries of innovation, reliability, and efficiency in the aerospace industry. As space exploration endeavors expand and evolve, the demand for cutting-edge hydraulic cylinder solutions will remain essential in supporting the next generation of space missions and scientific discoveries.